Why Consider Auto-Cushioning Pneumatic Cylinders?
We highlight the benefits of auto-cushioning in pneumatic cylinders and how to improve productivity and reduce maintenance.
Manually adjusting an air cushion on a pneumatic cylinder can be time consuming. This blog explains the benefits of considering an auto-cushioning option.
In the industrial world, the primary goal is often to boost productivity whilst reducing costs.
Pneumatic cylinders in particular have gained wide acknowledgement as being durable enough to withstand harsh environments alongside providing a high level of performance at a competitive rate.
However, they often require running actuators as fast as possible without introducing excessive shock or vibration to products and equipment, which can become demanding.
Due to operating at a higher speed and with potentially increased loads, engineers generally use an air cushion to avoid any lasting damage to the cylinder.
The issue is that the manual adjustment of these end-position cushions require time and using directly fitted flow regulators costs up to ten times more than a standard elbow or straight fitting.
Experienced maintenance technicians are required to adjust the air-cushion valves, depending on the cylinders operating pressure, speed and load. Once these parameters are changed, the air cushions then need to be reset for each job in order for the machine to run efficiently.
Manually adjusting the air cushion is not only time consuming but it can put pressure on the technicians to complete the task as quickly and efficiently as possible, as well as incurring unnecessary production costs.
With the introduction of a new type of air cushion which automatically adapts to changing conditions, the headache of manual adjustments is eliminated and productivity is increased, ultimately reducing maintenance costs.
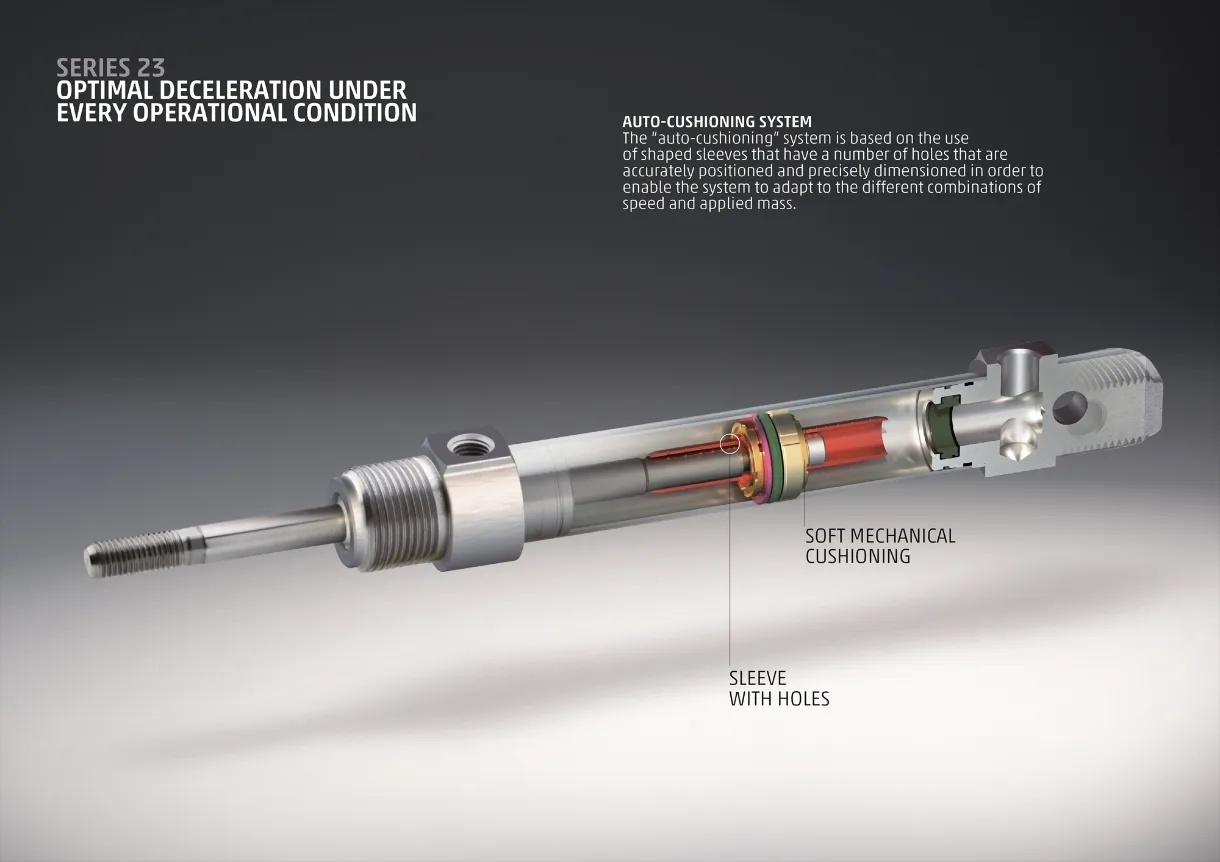
Camozzi Automation's Series 23 ISO 6432 pneumatic cylinders embrace the innovation of 'auto-cushioning'.
The 'auto-cushioning' system works the same as many conventional cushions, except instead of a needle valve, the air is exhausted with the use of shaped sleeves that have a number of holes accurately positioned with precisely set dimensions.
As the system cleverly adapts to various combinations of speed and applied mass, the self-adjusting cushion is a 'fit-and-forget' feature. Eliminating the need to regulate settings, the Series 23 pneumatic cylinders are ultimately tamper proof, offering a long, maintenance-free service life.
Whilst the cylinder benefits from a smooth, jolt-free movement, the reduction in vibrations and noise is also noticeable. Despite appearing less intrusive, the cushions guarantee higher reliability and constant performance over time.
If the parameters such as friction and pressure change, the self-adjusting cushions ensure proper deceleration every time. Reducing the acceleration forces acting on components and workpieces, the appearance of wear and tear is reduced and time-consuming vibration is minimised.
The series 23 is suitable for use in many industrial applications, especially if working conditions vary. Reducing the installation and commissioning times, the 'auto-cushioning' system provides a cost-effective alternative to manually adjustable cylinders.